|
Post by smlmike on Aug 31, 2015 14:34:02 GMT -5
The flywheel was what was very warm to the touch after sitting about 10 mins while talking to the mechanic. So the stator. It's a 2004 not sure what kind of hours it has on it? Like I said NO wires were visible melted.
|
|
|
Post by Pete D. on Aug 31, 2015 15:19:09 GMT -5
Doesn't surprise me. But keep in mind that with the motor cover on, the flywheel will stay warm for HOURS after the motor has been cut off. Kinda like the hood of a car.
|
|
|
Post by formula180 on Sept 1, 2015 10:11:37 GMT -5
I am not a mechanic, but I read this about my 50 hp Honda: "Early on, the mechanic at a sportfish camp in Hakai (running Honda 50s on 17' Boston Whalers) told me that the charging coils would go after 500 hours, and that is exactly what happened. From a reliability stand point that is not good. Too much heat over a period of time will degrade the insulation on the wire and the winding's short out. They should be looking at this type of problem and up grading the coils with a higher temperature wire.
|
|
|
Post by Pete D. on Sept 2, 2015 10:41:42 GMT -5
I am not a mechanic, but I read this about my 50 hp Honda: "Early on, the mechanic at a sportfish camp in Hakai (running Honda 50s on 17' Boston Whalers) told me that the charging coils would go after 500 hours, and that is exactly what happened. From a reliability stand point that is not good. Too much heat over a period of time will degrade the insulation on the wire and the winding's short out. They should be looking at this type of problem and up grading the coils with a higher temperature wire. I don't think its the wire that is the issue. Honestly, Id ALWAYS go with CDI electronics aftermarket outboard electronics. They are about 3/4-1/2 the price of the manufacturers, and they are also engineered to run better and last longer. For instance: Mercury has coated their stator windings with black epoxy for years. The issue with this is it heat soaks the coils in the windings causing them to prematurely fail. So, the replacements are just annealed wire wound around the stator base with no coating. CDI noticed this from the get-go and NEVER coated their stators. I have also seen shops very precisely drill holes into the flywheel to allow the heat to escape better through it. Some companies have even put out technical service bulletins to replace the flywheels with ones that have the "cooling holes" casted into them. Lots of heat goes straight up to the top of the outboard, where all the 'spensive electronics are, all covered up in a wind resistant insulated cowling!!
|
|
|
Post by getlinewet on Sept 2, 2015 12:24:27 GMT -5
Questions: (1) Is the stator the same as the charging coil I referred to? I wiki'ed the term and I would guess the answer is yes. (2) I've got 465 hours on my honda 50. Should I replace it now or should I wait for the charging coil (stator?) to go and be on guard for symptoms of failure?
|
|
|
Post by formula180 on Sept 2, 2015 19:04:18 GMT -5
We don't know the heat conduction properties of the black epoxy but they probably coated the stator with the epoxy to act as a heat sink. The thermal conductivity of epoxy is 2.2 while air is .1. www.epoxies.com/_resources/common/userfiles/file/managing_heat_transfer_potting_compounds.pdfHigh temperature wire can have several types of coatings or multiple coatings to provide higher temperature operation. Some engineer failed to run a reliability test to determine the mean time before failure. You could probably take the stator to a motor repair facility and have them rewind the stator with higher temperature wire. It is also possible to contact EDC and find out what the wire temperature rating is of the wire they use. Is there any outboard that the stator is not mounted in the flywheel? None that I know of, so this looks like a Yamaha problem. Not something you would want to fail while running offshore and why you see two Yamaha outboards and only one Mercury on most offshore boats.  If 500 hours is the MTBF, it would be safe to change the stator which will prevent damage to the voltage regulator and other electronics.
|
|
|
Post by formula180 on Sept 3, 2015 0:21:04 GMT -5
From a reliability stand point that is not good. Too much heat over a period of time will degrade the insulation on the wire and the winding's short out. They should be looking at this type of problem and up grading the coils with a higher temperature wire. They are about 3/4-1/2 the price of the manufacturers, and they are also engineered to run better and last longer. For instance: Mercury has coated their stator windings with black epoxy for years. The issue with this is it heat soaks the coils in the windings causing them to prematurely fail. So, the replacements are just annealed wire wound around the stator base with no coating. CDI noticed this from the get-go and NEVER coated their stators. The windings are coated to act as a heat sink and increase the MTBF, therefore they cost more. The windings are set in a form and the epoxy is applied and then the form is set in a vacuum chamber to draw all the air out between the windings and let the epoxy encapsulate the coils. Then the unit is placed in a heat chamber to cure and harden the epoxy. The wire has to have a coating or the windings would short out. As the coils age and the insulation deteriorates, windings will start to short out which draws more current and they self destruct. Maybe the hood needs a vent with a Rotron fan to reduce the heat or just run with the hood off. 
|
|
|
Post by Pete D. on Sept 3, 2015 16:51:24 GMT -5
|
|
|
Post by formula180 on Sept 3, 2015 17:27:34 GMT -5
Looks like a marketing sales pitch. All they have done is go to a higher temperature wire which is good.
The sloppy windings in the first picture is poor workmanship and shouldn't pass QC at most places.
Still adding the epoxy encapsulation of the coils would increase the MTBF further but at the same time increase cost.
|
|
|
Post by smlmike on Sept 3, 2015 18:04:43 GMT -5
Wouldn't vents in the top allow moisture in also? That wouldn't be good. Maybe some type of automatic vent?
|
|
|
Post by formula180 on Sept 4, 2015 12:54:03 GMT -5
Run with the hood off to see how much your top end speed increases. It looks like the stator has two outputs with one for charging the battery and one for the motor electronics. So you could pull the plug of the stator and measure the wire resistance. As the stator starts to go bad, the resistance will drop as the windings start to short out due to deterioration. Wouldn't be a bad test to do each year for the upcoming season. I assume you have an hour meter which is nice for motor maintenance. I would also add a voltmeter to monitor the condition of your batteries. I always liked VDO gauges. You could use a toggle switch to select the motor battery or the trolling motor battery. www.ebay.com/itm/like/281739864371?ul_noapp=true&chn=ps&lpid=82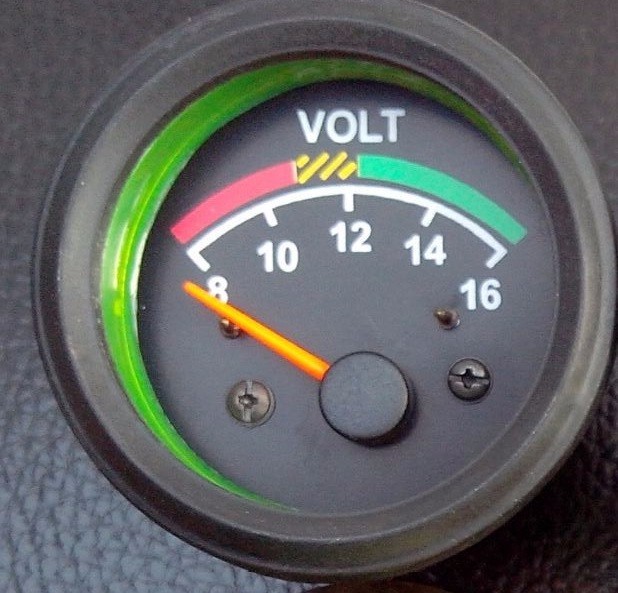 After some thought, it is probably best to get their marine gauges: marine.vdo-gauges.com/
|
|
|
Post by Pete D. on Sept 5, 2015 8:01:30 GMT -5
Yes but resistance is not a tell all for a stator. I have rewound numerous stators and believe me, I have seen loose and sloppy wiring in more than we would like to admit. The best thing to do is buy a DVA adaptor for your multimeter and check all stator leads according to the spec sheet that CDI has published. This will tell you the voltage output of the stator and that is the most accurate way to diagnose an electrical issue in an outboard motor. It's all right here issuu.com/cdielectronics/docs/troubleshootingguideCan't tell you how many people I know that have had shops mid diagnose and swap out good ignition parts because they failed To do these simple And straightforward tests. Just buy a DVA meter and be done with it.
|
|
|
Post by fujimo on Sept 5, 2015 8:16:12 GMT -5
one thing about this is yall must not like to fish like I do get someone that knows about it and get it fixed dang lmao
|
|
|
Post by Pete D. on Sept 6, 2015 21:22:39 GMT -5
one thing about this is yall must not like to fish like I do get someone that knows about it and get it fixed dang lmao I like knowing my outboards in and out. I also like wiring up all my electronics etc. in my boats. Sure as hell dont like paying those $85 an hour shop prices, and paying MSRP for shop parts. ESPECIALLY if I owned a Yamaha!!! To each their own I guess. I am a constant tinkerer. Often times you can find me on my boat, on the trailer, in my front yard. 
|
|
|
Post by fujimo on Sept 7, 2015 5:23:37 GMT -5
make since to me I don't pay retail for much myself but I do have a lot of connections for getting what I need done.
|
|